- 5Sって結局何?意味ある?
- 5S活動ってどう進めればいいかわからない
今回の記事はこのような方へ向けて書きました。
こんにちは!クマペイです!
工場勤務をしているとかならず聞くワード「5S」
ことあるごとにやれと言われ、報告をさせられる。
末端社員からすると、すごいやらされ感ありますよね。それでも僕は5Sをやることをオススメします。
「面倒くさいな〜きれいにしとけばいいんでしょ?」
こう思っている方も多いと思います。
かんたんに言えばそうなのですが、何も考えずに掃除をして自分の時間を消費するのはもったいないです。
会社のために取り組まなきゃ!と思うとなんか嫌なので←
自分のために取り組みましょう。
5Sに取り組むことで、当然工場の生産性が上がりますが、現場作業者にとっての本質はそこではありません。
僕が5Sをオススメする本当の理由は「楽に作業ができるから」と言う部分になります。
5Sとは
5Sは「整理(seiri)」「整頓(seiton)」「清掃(seisou)」「清潔(seiketu)」「躾(situke)」の頭文字を取った活動を指し、製造業や医療、様々な職場で業務改善を行う手段の一つとして用いられているものです。
また5Sの中に3S(整理・整頓・清掃)があることも理解しておきましょう。
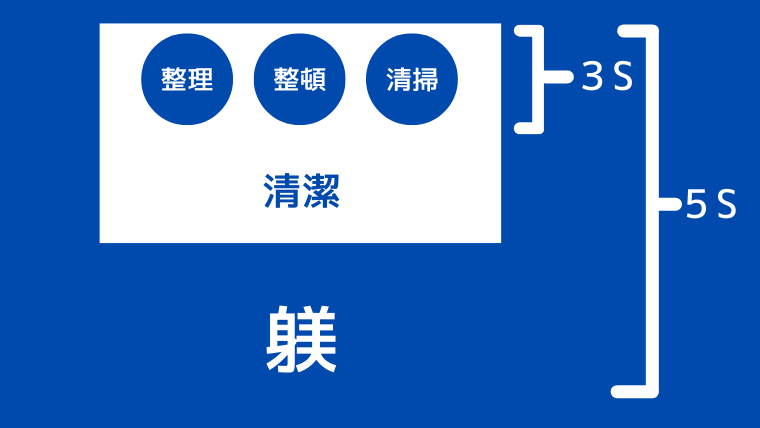
ではそれぞれの意味を解説していきます。
整理
必要なモノだけがある状態にすること。
不要なものを処分し、モノを減らすことで、ものを選ぶ回数が減り、きれいな状態も維持しやすくなります。
整頓
モノの場所をさだめること。
皆さんにも住所があるように、モノにも住所を与えてあげましょう。
モノをなくすリスクや探す手間をなくすことができます。
清掃
掃除をすること。
使用するものや職場をきれいな状態にし、作業しやすい環境を作ります。
清潔
「整理・整頓・清掃」3Sの維持とルール・仕組みの標準化。
清掃と混同されがちな項目です。
私も配属当初は清掃と清潔の違いがわからなかったのですが、清潔はルールだと思ってもらえれば大丈夫です。
定期的な現場の点検やルールの見直しをしていくことで達成されます。
躾(しつけ)
3Sが定着し、ルールを守れる状態になっていること。
躾(しつけ)という表現だと厳しく感じるかもしれません。
習慣・風土という表現の方がしっくり来ると思います。
表にまとめるとこんな感じ
項目 | 意味 | 英語 |
整理 | 必要なモノだけがある状態にすること | Sorting |
整頓 | モノの場所をさだめること | Setting-in-Order |
清掃 | 掃除をすること | Shining |
清潔 | 3Sの維持とルール・仕組みの標準化 | Standardizing |
躾 | 3Sが定着し、ルールを守れる状態になっていること | Sustaining the Discipline |
英語の場合の表現もまとめました。
英語でもうまいこと5Sになっています。
5Sの効果
言葉の意味がわかったところで、5Sの効果について見ていきましょう。
5Sを進めるとこのような効果が見込めます。
- 作業効率が上がる
- 品質が上がる
- 安全に作業ができる
- 楽に作業ができる
なんとなくやっている5Sですが、しっかり行えばちゃんと自分の仕事が楽になります。
それぞれ見ていきます。
作業効率が上がる
モノが必要な場所に必要なだけある。
この状態は思っている以上に作業がしやすくなります。
モノを探す時間というのは本当に無駄な時間です。
目的のモノが見つからなくてイライラするし、いるいらないの判断に脳も疲れてしまいます。
「気づくと机がぐちゃぐちゃになっているあなたへ」の著者であるリズ・ダベンポートさんによると平均的なサラリーマンは年間1500時間もモノを探しているとのことです。
1500時間もモノを探すより、数時間で5Sを行い、働きやすい環境を作ったほうが断然オススメです。
品質が上がる
製品を作る、直す、メンテナンスするなどのすべての仕事の成果の品質が上がります。
どんな単純作業にもミスはつきものですが、5Sを行い作業環境を整えることでミスのリスクを最小限にすることが可能です。
ミスの最小限化によって品質が上がるということです。
安全に作業ができる
作業場所にモノがなくなるので、なにかにつまずいたりする危険がなくなるのは当然ですが、さらなる効果として、作業の工程が減るというのがあります。
職場の5Sを進めることで本来やる必要がない作業がなくなり、移動や工程が減ります。
人間が動くということは常に何かしらのリスクがあるものです。
例えば本を読むという動作にさえ、指を切ることや落とした本を拾おうとして腰を壊してしまうなどの可能性が潜んでいます。
自分が怪我をしないという目的で5S活動をしようと思えば有意義な活動にできそうです。
楽に作業ができる
最後に楽に作業ができるようになります。
5Sにより作業しやすく、安全で、高品質な成果が出せる環境を整えることで、心身ともに気楽に仕事を続けることができます。
上司に怒られることは減り、怪我もしない、そして無駄な作業が減るので定時帰りができる。
最高です。
そしてこれらの活動は会社の経費を使ってできます。
会社の金をバンバン使ってより楽で快適な職場を目指していきましょう。
5Sの失敗しない進め方
5Sを闇雲に進めてもただの掃除になってしまい、結局時間だけ使うことになり、失敗となります。
そこで重要なのが進め方です。
私の上司には具体的な指示もなく「5Sやっといて」と言ってくる人がいますが、こちらとしては困ってしまいます。
学校で教えてくれないのに、社会に出たら当然のように言われても・・・状態です。
ということで、ここで進め方を確認し失敗のリスクを下げて行きましょう。
流れとしてはこのようになっています。
「整理・清潔」⇒「整頓・清潔」⇒「清掃・清潔」⇒「躾」
ちなみに、3Sである整理・整頓・清掃に清潔がセットになっている理由は、それぞれにルールを決める必要があるからです。
整理・清潔(ルール決め)
まずは整理から。
いらないものを捨てて必要なものだけがある状態にします。
整理のポイントは現在どのような作業をしてどのようなモノが必要かリストにすること。
業務の可視化とも言えます。
他にも赤札作戦を行うことも効果的です。
こうすることで必要なモノが明らかになり、どんなモノを優先的に使っているのか見え、整理のルールを作ることができます。
モノのリスト化
例えばこんなふうにリストにします。
作業名 | 作業頻度 | モノ |
作業1
|
高
|
13mmスパナ |
プラスドライバー | ||
マイナスドライバー | ||
ウエス | ||
作業2
|
中
|
ラチェットレンチ |
13mmソケット | ||
プラスドライバー | ||
作業3
|
低
|
パソコン |
プリンター |
リストにしてみるポイントは、「同じモノを使っていないか」、「作業頻度が高い作業のモノの置き場は良いか」などの視点で見ると改善点が見えてきます。
今回のリストから、作業1と作業2で同じ工具を使っているから工具置き場をまとめることができる!ということがわかりますね。
2つあった工具が一つになることでモノの紛失防止にもなります。
赤札作戦
チームで作業場所を見回り、いらないものに赤札を貼っていく方法。
赤札を貼ったものに対して、改善を行うという流れです。
普段作業している人以外が作業場所をみることで新たな視点で5Sを進めることができます。
5Sの文化がないところで、いきなり全員で赤札作戦をやるのはちょっとハードルが高いですが、少人数の有志で始めてみても赤札作戦の成果は実感できると思います。
普段とは違う職場を見るだけでも気付けることはたくさんあるので、ぜひ実行してみてください。
整頓・清潔(ルール決め)
いらないモノがない状態になったら、モノの場所と数量を決めていきます。
ここでも整理の段階で行った業務の可視化が活きてきます。
場所と物を決めたら、テプラーや札などでそこに何が置かれるのか明記していきます。
そうすることで必要なとき、必要なモノが決められた場所に必要なだけある状態にできます。
作業で無駄な時間は物を探す時間です。整理をしっかり行うことで物を探すという無駄な時間を減らすことが可能です。
清掃・清潔(ルール決め)
ゴミや汚れがないキレイな状態を目指し、掃除をしましょう。
清掃は特にルール決めが大切です。
- 頻度
- 程度
- 担当
これらの項目を網羅した表を作ると作業者全員がルールを認識できて清掃の定着に繋がります。
3Sの維持
ポイントはこちら
<div class=”simple-box4″><p>定期的な点検と無駄な業務をしない</p></div>
まず、3Sを維持するためには定期的な点検が必須です。
チームで働いている場合は持ち回りで行い、一人作業の場合は自分の仕事の範囲をきちんと点検するように心がけましょう。
私の職場では月に一度5Sと安全状況を確認する取り組みを行っています。
しかし、職場内で取り組んでいる場合はいいですが、そうでない場合、高い意識を持ち続けるのは容易なことではありません。
ですので、そもそも無駄な業務はしない。
という意識を持って日々仕事ができると5Sの手間も減りますし、効果も高まります。
まとめ
工場勤務なら必ずやることになる5S。
イヤイヤやってもいいですが、せっかくなら自分が楽に働けるように会社の金を使って改善して行きたいですね!
工場勤務の特徴である決まった業務だからこそ、どんどん効率化してプライベートの充実に人生の時間を使っていきましょう。
以上!